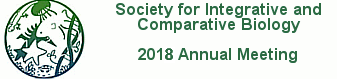
Meeting Abstract
Recent progress in manufacturing has led to rapid rise in the use of physical models for testing hypotheses about the form and function of biological structures. However, natural architectures are often complex structurally and heterogeneous materially making them difficult to manufacture through traditional approaches. One such intricate structure is the wing of an insect which has the added complication of embedded microchannels for fluid flow and gaseous exchange. In this study, we show three fabrication strategies – soft lithography, thermoforming and multi-material 3D printing. for rapidly prototyping wings with high fidelity. We demonstrate each of the above techniques by prototyping wings at 1X (soft lithography), 10X (thermoforming), and 100X (3D printing) scales drawing inspiration from the green darner dragonfly, Anax junius, as our model organism. Using these physical models, we test the following hypotheses that, 1) fluid flow within the veins modulates the macro mechanical properties (stiffness, damping) of the wing, and that 2) fluid flow modulated wings affect flight performance. Our preliminary experiments reveal that fluid flow can play a major role in modulating the stiffness and damping of the wing. We are currently performing complementary experiments on biological samples to measure the range of flow rates and their scaling with size. As our next steps, we aim to build experiment setups to test the flapping performance of the robotics prototypes across the biologically relevant range of frequencies in our custom wind tunnel. We believe that such high fidelity physical models are critical to revealing novel insights into the functional morphology and biomechanics of complex biology structures by serving as faithful test platforms for hypotheses testing.