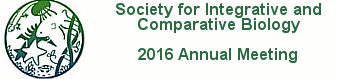
Meeting Abstract
Inadvertent collisions with obstacles are inevitable for small insects flying in the natural world, where they are buffeted by unpredictable airflows and confronted with dynamic obstacles that can thwart even the best flight control systems. Despite the prevalence of collisions among insects, few studies have examined their consequences, or explored morphological features that help minimize their potentially detrimental effects. The wings of bees, and likely other insects, collide with vegetation frequently (once per second on average), and over time these collisions cause the wings to wear down, decreasing flight performance and increasing mortality. Prior work has shown that wasp wings contain a flexible resilin joint positioned distally along the leading edge of the wing, which allows the wing tip to reversibly collapse during collisions, thereby mitigating wing damage. To characterize the material properties of the costal break, we performed displacement-controlled bending tests of wasp wings. Stress-strain curves reveal that this joint exhibits non-linear, strain-weakening behavior, with an initial stiffness that rapidly diminishes beyond a particular load threshold. Inspired by the beneficial role that this joint plays in damage mitigation for wasps, we used a PC-MEMS manufacturing process to build similar strain-weakening flexure hinges into the artificial wings of an insect-scale microrobot. In addition to promising increased wing longevity for flapping micro-aerial vehicles, incorporating these bio-inspired joints into a robotic platform has enabled us to test the additional hypothesis that collapsible wing joints may also facilitate insect flight control in cluttered environments, by damping wing collision forces that are transmitted to the body.