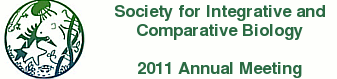
Meeting Abstract
S5.3 Wednesday, Jan. 5 At-scale artificial insect wings by microfabrication techniques TANAKA, H*; WOOD, R J; Harvard University; Harvard University tanaka@seas.harvard.edu
Insect wings have complex morphologies such as vein networks and 3-D surface profiles. Since wings lack muscles to actively change the wing shape, these wing structures determine the stiffness and hence the deformations due to fluid and inertial forces experienced during flight. It is reasonable to assume that the insect flight apparatus has evolved to enhance flight performance, but the contributions of these aspects of wing morphology to flight function are still unclear. To explore this question and simultaneously elucidate design principles for robotic insects, we fabricated at-scale artificial insect wings and compared different wing designs using mechanical flappers. Artificial models allow us to study the role of key features in otherwise overly-complicated natural wings and test them under controlled conditions. Technical challenges for fabrication of at-scale wings include the creation of micron-order veins and membranes onto various 3D surface topologies. Artificial wings were realized by a polymer micromolding technique, in which polymer veins and membrane are simultaneously formed with micromolds. The micromolds were created by laser scanning ablation or anisotropic plasma etching. In this talk, two examples of fabrication and experiments using artificial insect wings, mimicking a hoverfly and swallowtail butterfly, will be demonstrated. For the swallowtail butterfly, the effect of venation on flight performance was investigated using a flight-worthy flapping-wing robot. For the hoverfly, the effect of 3-D corrugation on stiffness and the resulting deformation was examined using a tethered flapper.