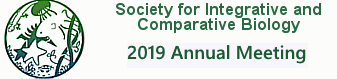
Meeting Abstract
Flapping insect wings bend and deform during flight. Recent evidence suggests this deformation improves power economy and reduces the cost of locomotion. To assess this hypothesis, we drive a hawkmoth M. Sexta wing with single degree-of-freedom rotation using a DC motor and calculate the corresponding mechanical power requirements. We consider a 60-degree rotation amplitude and a wide range of flapping frequencies. Wing moments are measured via a custom torque transducer and the flap angle is measured using an optical encoder. The two measurements are utilized to estimate the mechanical power required to flap the wing. Experiments are conducted in-air and in-vacuo to provide insight into inertial-elastic and aerodynamic energetics. Our results suggest that at a typical flap frequency of 25 Hz, the wing requires maximally 40 mW in-air and 30 mW in-vacuo. Peak moments corresponding to these power draws are 0.55 mN-m and 0.35 mN-m, respectively. We estimate that for the in-vacuo case, the real flexible wing requires only 75% the peak power relative to an idealized rigid wing. Next, we identify the root-mean-square (RMS) value of mechanical power as a function of flapping frequency, where the RMS value of power is a proxy for total energy expenditures. We find that over the entire 15-30 Hz flap frequency range, the RMS mechanical power of the wing is higher in-air than in-vacuo. Furthermore, we observe that for the in-air response, the RMS power follows a non-monotonic trend, where it decreases temporarily as the flapping frequency is increased beyond 1/3 of the wing’s second natural frequency. Thus, it is plausible that tuned structural compliance may facilitate the energy efficiency of flapping insect wings.