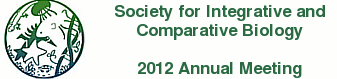
Meeting Abstract
P3.141 Friday, Jan. 6 Measuring cost of flight associated with varying kinematics in a robotic bat wing BAHLMAN, Joseph Wm*; SWARTZ, Sharon M; BREUER, Kenny S; Brown University; Brown University; Brown University joseph_bahlman@brown.edu
Bats inhabit a variety of realized ecological niches that require diverse aspects of flight performance. Depending on its niche, a bat may be required to perform complex maneuvers, commute or migrate long distances, carry heavy loads, fly very fast, hover, or various combinations of these. These behaviors arise from distinct wing kinematics that produce distinct patterns of aerodynamic forces while incurring a mechanical cost. The mechanical cost to flap results, in part, because bats possess relatively heavy wings, ~12% of body mass, and their motion incurs inertial and aerodynamic costs as they move the wings through a fluid medium. To understand the mechanical cost associated with different flapping kinematics we constructed a robotic bat wing, with seven joints actuated by three servo motors. This flapper design allows the shoulder to move dorsoventrally and anterioposteriorally, and the elbow and wrist to flex and extend simultaneously, which retracts and extends the entire wing. These degrees of freedom allow us to test a variety of kinematic parameters including: wing beat frequency and amplitude, stroke plane, downstroke ratio, and retraction/extension, all across a realistic range for our model species, Cynopterus brachyotis. The robotic wing was mounted in a windtunnel on a two-axis force transducer that measures aerodynamic force; torque and power were measured from the servo motors. For each kinematic parameter we quantified the lift and drag/thrust generated per wingbeat, mechanical work per wingbeat, and average flapping power. Our model showed how aerodynamic force generated, and work and power cost change with different kinematic parameters.